Selain alasan yang disebutkan di atas, bagian aluminium berubah bentuk selama pemrosesan. Dalam operasi yang sebenarnya, metode operasi juga sangat penting.
Untuk bagian dengan tunjangan pemesinan yang besar, agar memiliki kondisi disipasi panas yang lebih baik selama proses pemesinan dan menghindari konsentrasi panas, pemesinan simetris harus digunakan selama pemesinan. Jika ada lembaran tebal 90mm yang perlu diproses hingga 60mm, jika satu sisi digiling dan sisi lainnya digiling segera, dan ukuran akhir diproses sekali, kerataan akan mencapai 5mm; Jika pemrosesan simetris umpan berulang digunakan, masing -masing pihak diproses dua kali ukuran akhir dapat menjamin kerataan 0,3mm. Jika ada banyak rongga di bagian pelat, tidak disarankan untuk menggunakan metode pemrosesan berurutan rongga-oleh-rongga selama pemrosesan, karena ini akan dengan mudah menyebabkan kekuatan yang tidak merata dan deformasi bagian. Pemrosesan multi-lapisan diadopsi, dan setiap lapisan diproses ke semua rongga pada saat yang sama sebanyak mungkin, dan kemudian lapisan berikutnya diproses untuk membuat bagian-bagian ditekankan secara merata dan mengurangi deformasi.
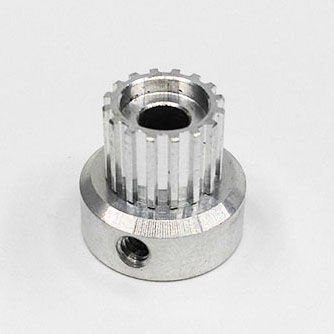
Kurangi gaya pemotongan dan memotong panas dengan mengubah jumlah pemotongan. Di antara tiga elemen jumlah pemotongan, jumlah pemotongan kembali memiliki pengaruh besar pada kekuatan pemotongan. Jika tunjangan pemesinan terlalu besar, gaya pemotongan pass terlalu besar, yang tidak hanya akan merusak bagian -bagian, tetapi juga mempengaruhi kekakuan spindel alat mesin dan mengurangi daya tahan alat. Jika Anda mengurangi jumlah pisau kembali, efisiensi produksi akan sangat berkurang. Namun, penggilingan berkecepatan tinggi digunakan dalam pemesinan CNC, yang dapat mengatasi masalah ini. Sementara mengurangi jumlah yang menarik, selama umpan meningkat secara bersamaan dan kecepatan alat mesin meningkat, gaya pemotongan dapat dikurangi sambil memastikan efisiensi pemrosesan.
Juga perhatikan urutan pisau. Pemesinan kasar menekankan peningkatan efisiensi pemesinan dan pengejaran tingkat penghapusan per satuan waktu. Umumnya, penggilingan atas dapat digunakan. Artinya, bahan berlebih pada permukaan kosong dihilangkan pada kecepatan tercepat dan waktu terpendek, dan kontur geometris yang diperlukan untuk finishing pada dasarnya terbentuk. Penekanan finishing adalah presisi tinggi dan berkualitas tinggi, dan penggilingan down harus digunakan. Karena ketebalan pemotongan gigi pemotong secara bertahap berkurang dari maksimum ke nol selama penggilingan turun, tingkat pengerasan kerja sangat berkurang, dan pada saat yang sama tingkat deformasi bagian berkurang.
Benda kerja berdinding tipis dideformasi karena penjepit selama pemrosesan, dan bahkan finishing tidak dapat dihindari. Untuk meminimalkan deformasi benda kerja, bagian yang mendesak dapat dilonggarkan sebelum ukuran akhir dari proses finishing tercapai, sehingga benda kerja dapat dikembalikan ke bentuk aslinya secara bebas, dan kemudian sedikit dikompresi, tunduk pada penjepit yang kaku kaku yang kaku kaku yang kaku secara kaku secara kaku kaku yang kaku kaku yang kaku dengan kaku yang kaku dengan bebas dengan kaku kaku Dari benda kerja (sepenuhnya dengan tangan), efek pemrosesan yang ideal dapat diperoleh dengan cara ini. Singkatnya, titik aksi gaya penjepit paling baik pada permukaan pendukung, dan gaya penjepit harus bertindak ke arah kekakuan benda kerja yang baik. Di bawah premis memastikan bahwa benda kerja tidak mengendur, semakin kecil kekuatan penjepit, semakin baik.
Saat pemesinan bagian dengan gigi berlubang, cobalah untuk tidak membiarkan pemotong penggilingan terjun langsung ke bagian seperti bit bor, menghasilkan ruang chip yang tidak mencukupi untuk pemotong penggilingan, penghapusan chip yang tidak halus, dan overheating, ekspansi, dan keruntuhan pahat. Fenomena yang tidak menguntungkan seperti pisau patah. Pertama, bor lubang dengan bor dengan ukuran yang sama dengan pemotong penggilingan atau satu ukuran lebih besar, dan kemudian menggilingnya dengan pemotong penggilingan. Atau, perangkat lunak CAM dapat digunakan untuk menghasilkan program pemotongan spiral.